Forklift G5T16 micro switch is a device used to detect and control forklift movement. Its main function is to trigger a signal when the forklift moves to a specific location so that corresponding operations or stops can be performed.
Forklift G5T16 micro switch is a device used to detect and control forklift movement. G5T16 micro switch is usually designed as a mechanical switch, which can trigger an electrical signal in a specific position or state by being connected to the movement of the forklift. These signals can be used by the forklift’s control system to perform corresponding actions, such as stopping motion, changing direction, or performing other tasks.
The application of G5T16 micro switch in forklifts helps to improve the accuracy and safety of forklift operations. By correctly placing and configuring microswitches, functions such as precise positioning, safe stopping, and automated control can be achieved to optimize forklift performance. These devices play a key role in ensuring that forklifts operate according to predetermined plans during work, avoiding accidents and improving efficiency.
G5T16 micro switch usually consists of a mechanical arm and a movable contact. When the forklift contacts the robotic arm of the G5T16 micro switch during motion, the robotic arm will be pushed. The movement of the robotic arm causes the contacts within the microswitch to operate. G5T16 micro switch has two types: normally closed and normally open. Under normal circumstances, if it is a normally closed type, the contact is closed, while if it is a normally open type, it is open.
When the contact of the G5T16 micro switch moves, an electrical signal will be generated. This signal can be connected to a control system, such as a forklift’s controller or electrical system. After receiving the signal from the micro switch, the forklift’s control system can perform corresponding operations, such as stopping movement, changing direction, or performing other specific actions.
The forklift G5T16 micro switch enables the forklift to make corresponding control responses at a specific position or when specific conditions are reached through mechanical triggering and electrical signal transmission. This helps ensure that the forklift can perform its tasks safely and accurately during operation.
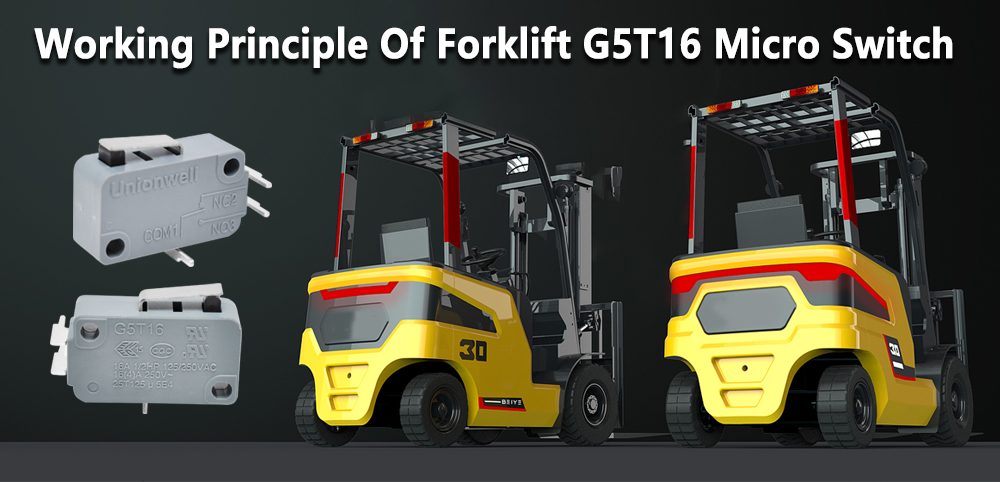
How can the G5T16 micro switch improve the performance of forklifts?
The use of G5T16 micro switches in forklifts can improve performance and safety. The application of micro switches in forklifts can help improve the accuracy, safety and efficiency of operations, thereby improving the overall performance of the forklift. Forklifts can stop movement quickly and safely to avoid collisions, accidents or other potential hazards. Micro switches and other safety devices play an important role in achieving a safe stop of the forklift.
-
Precise positioning of forklift
The G5T16 micro switch can be placed in key parts of the forklift to detect specific positions or states. Through accurate position detection, forklifts can load, unload, position and move goods more accurately, improving the accuracy and efficiency of operations. Micro switches are widely used to detect the position of forklifts. By installing microswitches at key locations on the forklift, the corresponding signal can be triggered when the forklift reaches a specific position, thereby achieving an accurate stop.
Advanced forklifts are equipped with automatic navigation systems that can use various sensors (such as lidar, cameras, etc.) to perceive the surrounding environment in real time and navigate according to predetermined paths. Such a system can accurately navigate a forklift to its target location without the need for human intervention. The use of global satellite navigation systems and other positioning technologies can improve the positioning accuracy of forklifts in indoor and outdoor environments. This is particularly important for large warehousing sites and complex operating environments.
Laser rangefinders and other distance sensors can be used to measure the distance between a forklift and a target location in real time, helping the forklift to dock more accurately. Vision systems, such as cameras and image processing software, can be used to detect the surrounding environment and target locations. These systems can determine the location of a forklift through image analysis and provide real-time feedback to ensure accurate docking.
-
The forklift stops safely
The G5T16 micro switch can be used to monitor the movement status of the forklift. When the forklift reaches a predetermined position or an abnormal situation occurs, the micro switch can trigger an emergency stop to prevent potential accidents or collisions. This helps improve workplace safety. Forklifts are usually equipped with an emergency stop button that the driver can press immediately in the event of an emergency. This button triggers the forklift’s emergency braking system to quickly stop the forklift.
Forklifts are equipped with collision sensors that can sense collisions with other objects. When a collision sensor detects a collision, it can trigger the forklift’s parking mechanism to prevent further collision and damage. Micro switches can be used to detect the position, status or movement of a forklift. When certain conditions are triggered, the microswitch can send a signal to the control system, requiring an emergency stop.
Forklifts may be equipped with autonomous navigation systems that, by monitoring their surroundings in real time, can identify potential hazards and trigger safe shutdown procedures if necessary. A PLC is a computer system used to control forklift operations. In the PLC, it is possible to program the conditions for a safe stop and perform emergency braking when these conditions are met. Forklifts are equipped with driver assistance systems such as reversing cameras or sensors. These systems can help drivers identify potential obstacles, thereby reducing the risk of collisions and accidents.
-
Automated control of forklifts
The micro switch is integrated with the forklift control system and can be used for automated control. By detecting the status of the forklift, the control system can make real-time decisions, such as automatically switching the position of the forks or adjusting speed, thereby optimizing operations and increasing work efficiency. Forklifts are often equipped with autonomous navigation systems that use a variety of sensors to sense their surroundings and then use this information to plan and execute paths. Such systems enable forklifts to navigate autonomously and avoid obstacles.
Various sensors, such as laser sensors, ultrasonic sensors and cameras, can be used to detect objects, obstacles and landmarks around the forklift. These sensors provide real-time environmental information, allowing forklifts to make real-time decisions. Using advanced control software, forklifts can be programmed to perform specific tasks. This includes path planning, automatic parking, cargo stacking and other functions.
Using machine learning and artificial intelligence technology, forklifts can adapt to different work environments and tasks. This allows the forklift to improve its operation and decision-making capabilities through learning and adaptability. The control system of a forklift usually consists of a programmable logic controller and other integrated electronic devices. These systems are used to coordinate the various functions and tasks of a forklift.
By connecting to the Internet, the forklift can be remotely monitored and managed remotely. This allows the operator to remotely monitor the status, performance and position of the forklift and make necessary adjustments and controls. Automated forklifts are equipped with automatic charging systems that can automatically return to the charging station for recharging when needed. This way, the forklift can continue to perform its tasks without human intervention.
-
Energy saving and life extension of forklifts
Microswitches can help optimize energy use in forklift automation systems. By precisely controlling the movement of the forklift when needed, unnecessary energy consumption can be reduced and energy efficiency improved. Additionally, microswitches help extend the life of your forklift by reducing wear and tear on mechanical components.
Automated control of forklifts refers to the use of advanced technologies and systems that enable forklifts to perform tasks with no or minimal human intervention. Automated controls can improve the efficiency, accuracy and safety of forklift operations.
-
Forklifts can reduce operating errors
The use of micro switches reduces the risk of human error. By automatically detecting the status of the forklift, micro switches can prevent actions from being performed at the wrong time or location, reducing the operator’s burden and improving operation accuracy. Forklift systems can be pre-programmed to perform specific tasks, such as automatic loading and unloading of goods, automatic stacking, etc. This reduces driver intervention and reduces task execution issues due to human error.
Forklifts equipped with collision sensors can detect surrounding obstacles. Once there is a risk of collision, the system can trigger an emergency stop to reduce the possibility of collision and damage. Reversing cameras, surround-view cameras and other visual assistance systems can help drivers see their surroundings more clearly and reduce operational errors caused by obstructed vision.
Application of micro switch in forklift
Micro switches have a variety of applications in forklifts, mainly by detecting the status, position or movement of the forklift to achieve precise control and improve safety. Forklifts can achieve high-precision limit detection to ensure that they can accurately stay at the target position when performing tasks. This is crucial to improving the operating efficiency, safety and automation level of forklifts.
-
Forklift limit detection
Micro switches are often used to detect the position of a forklift to ensure that the forklift stops at a specific location or performs a specific action. This helps to precisely control the movement of the forklift, ensuring it is in the correct position for loading, unloading or other operations. Forklift limit detection refers to detecting the position of the forklift by using devices such as sensors or switches to ensure that it stops at a specific position or performs a specific action. This helps with precise positioning, avoiding collisions and ensuring the forklift stays exactly where it’s supposed to when performing its tasks.
Micro switch is a device commonly used for forklift limit detection. By installing a microswitch at a specific location on the forklift path, when the forklift comes into contact with the microswitch, the switch triggers a signal to notify the control system to perform corresponding operations, such as parking or changing direction.
-
Forklift height detection
Micro switches can be used to detect the height of forklift forks when it comes to lifting and stacking goods. This is important to prevent excessively high or low fork heights and ensure that loading and unloading tasks are carried out at the appropriate height. Forklift height detection refers to measuring the height of the forklift fork arm or other parts by using sensors or other devices. This feature is important to ensure that the forklift can operate at the appropriate height when performing tasks, especially during cargo handling and stacking.
Laser sensors can be used to measure the distance between a forklift’s fork arm and a target location to determine the forklift’s height. This sensor typically emits a laser and measures the reflection time of the laser to calculate the distance between the forklift and the target. Ultrasonic sensors can detect distance by measuring the reflection time of sound waves. Installing ultrasonic sensors on the fork arms of forklifts can be used to detect the height of the ground or cargo.
-
Forklift collision detection
Micro switches can be installed on the structure of the forklift to detect if a collision occurs. In the event of a collision, microswitches can trigger an emergency stop to mitigate potential damage and improve operational safety. The integrated control system of the forklift can comprehensively utilize various sensor information and determine whether there is a risk of collision based on preset rules or algorithms to take appropriate measures. Installing anti-collision bars, guardrails or other protective devices on the structure of the forklift can slow down the force of the collision and reduce potential damage in the event of a collision.
Forklift collision detection refers to detecting the risk of collision between the forklift and the surrounding environment, objects or other forklifts through the use of sensors and other technologies, and taking appropriate measures to reduce potential damage. Collision sensors are sensors specifically designed to detect collisions. These sensors are typically mounted on the front, sides or other critical areas of the forklift and can sense when an object or obstacle is approaching and colliding with it.
-
Forklift pallet inspection
Install a microswitch on the forklift to detect the position and status of the cargo pallet. This is important to ensure that the forklift inserts the goods correctly and remains stable during transportation. A weight sensor installed on the fork arm or lifting system of the forklift can be used to detect the weight of the cargo pallet. This helps ensure that the forklift is not overloaded during handling. Capacitive sensors can be used to detect the position and shape of objects. Installing capacitive sensors on forklifts can be used to detect the shape and position of pallets.
-
Forklift safety door switch
Install a microswitch in the cab or other area of the forklift to detect whether the driver is in the correct position. This ensures that the forklift can only start and run under the right conditions, such as when a safety door is closed. The forklift safety door switch is a device used to monitor and control the status of the driver’s seat safety door.
The safety door switch is usually integrated into the driver’s seat. This switch detects whether the driver is in the seat. When the driver stands up or leaves the seat, the switch triggers a corresponding signal. The safety door switch is used to monitor the status of the forklift’s cab safety door. If the safety door is not closed properly, the switch will send a signal to notify the control system.
The driver’s seat switch and safety door switch are usually linked to the forklift’s electrical system. These switches can prevent the forklift from starting when the driver is not in the seat or the safety door is not closed, or trigger emergency braking while in operation. When it is detected that the driver is not in the seat or the safety door is not closed, the safety door switch may trigger a sound or light signal to remind the driver to take necessary safety measures.
-
Forklift traveling direction control
Micro switches can be integrated with the forklift’s control system to control the direction of travel of the forklift. By detecting the micro switch signal when the direction is switched, it can be ensured that the forklift turns correctly during operation. The forklift uses a steering wheel for manual control. By rotating the steering wheel, the driver can control the steering of the front wheels, thereby changing the direction of travel of the forklift.
Forklifts use a joystick or joystick system that allows the driver to change the direction and speed of the forklift by moving the joystick. On some forklifts, the foot pedals can be used to control forward, reverse, and braking. By adjusting the position of the foot pedal, the driver can change the direction of movement of the forklift. Advanced forklifts are equipped with automatic navigation systems that use sensors such as lidar and cameras to sense the surrounding environment and plan and adjust movement directions according to predetermined paths. This enables the forklift to navigate autonomously, avoid obstacles, and follow preset trajectories.
These applications help improve the accuracy, safety and efficiency of forklift operations, allowing forklifts to better adapt to different work scenarios and task requirements. Forklifts can efficiently detect cargo pallets, ensuring that pallets can be accurately inserted, lifted and transported during the handling process, improving the accuracy and safety of operations. This is critical for forklift operations in warehousing and logistics environments.