Working principle of IP67 microswitch for feed (grass) processing machinery
Feed (grass) processing machinery IP67 microswitch is a switch device used to control feed (grass) processing equipment. It is usually designed to detect or trigger small movements in a specific position or state. The role of IP67 microswitches in feed (grass) processing machinery can be to start, stop, or change the operating status of the machine to ensure that the equipment remains safe and effective during normal operation.
IP67 microswitches typically start or stop a circuit via physical triggering. When a component of the feed (grass) processing machinery reaches a specific position or state, the IP67 microswitch will be triggered and change the switch state.
The working principle of the IP67 microswitch for feed (grass) processing machinery is based on its design. It usually uses physical triggering to open and close the electrical contacts. IP67 microswitches usually contain a small arm or lever inside, called a movable arm. This movable arm is connected to a moving part of the feed processing machine. When this part moves to a predetermined position or reaches a specific state, the movable arm is triggered by mechanical force.
There is usually a trigger point at one end of the movable arm, which is affected by external forces during mechanical movement. When the trigger point is subjected to sufficient force or pressure, the trigger point will cause the internal electrical contacts of the IP67 microswitch to change through a mechanical mechanism.
The IP67 microswitch contains one or more electrical contacts, usually a pair of contacts. These contacts remain closed under normal conditions, forming an electrical circuit. When the IP67 microswitch is triggered, the mechanical mechanism causes the contacts to open or close, thereby changing the state of the circuit.
When the contacts of the IP67 microswitch change, the corresponding circuit status will also change. This can trigger relevant control signals, such as starting or stopping feed processing machinery, changing operating status, etc. The working principle of the IP67 microswitch for feed (grass) processing machinery is based on mechanical movement triggering changes in the state of electrical contacts to achieve control of mechanical equipment. This design is simple and reliable, and is suitable for application scenarios that need to trigger operations under specific conditions.
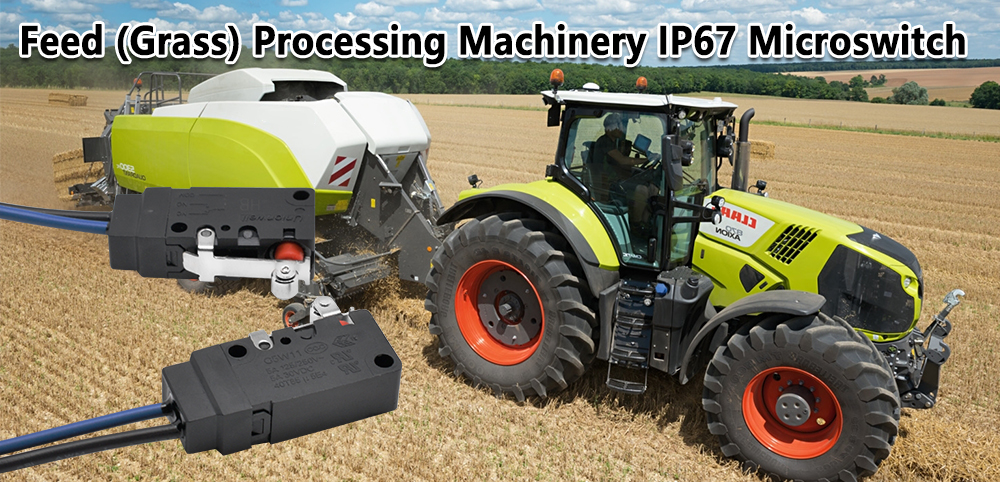
Position installation of IP67 microswitch for feed (grass) processing machinery
Microswitches are often installed at key locations on feed processing machinery, such as on rotating parts, moving conveyor belts or other moving parts. IP67 microswitches are usually designed to work in humid or dusty environments, so their location installation needs to consider IP67 and dustproof requirements. In feed processing machinery, the installation location of IP67 microswitches usually depends on the specific structure and operating process of the equipment.
Install the IP67 microswitch near the feed inlet or conveyor belt entrance of the feed processing machinery. This allows the flow of materials to be monitored and controlled during feed placement or delivery. If there are rotating parts or mechanical transmission systems in the feed processing machinery, you can consider installing IP67 microswitches at these critical locations to monitor the rotational movement and control related operations.
Install an IP67 microswitch near the discharge port or outlet of the feed processing machinery to trigger corresponding operations when the feed processing is completed, such as shutting down or switching to the next working stage. Feed processing machinery needs to be cleaned regularly. You can consider installing IP67 microswitches at the location of the cleaning device to ensure the safety and smoothness of the cleaning process. The control box or control panel of feed processing machinery is also a common installation location, so that microswitches and other control components can be easily integrated.
Design features of feed (grass) processing machinery
IP67 microswitches are usually designed to be compact, durable, and have certain dust-proof, IP67 performance to adapt to the working environment of feed processing machinery. The design features of feed (grass) processing machinery may vary depending on the type and purpose of the equipment. Feed processing machinery often needs to handle a variety of different feeds, including grass, hay, pellets, etc. Therefore, the structure of the machinery needs to be robust enough to cope with the forces and vibrations that may occur during the handling of different types and forms of feed.
Since feed processing machinery may be exposed to a variety of raw materials with different feed and moisture content, the parts of the machinery usually need to be made of corrosion-resistant, wear-resistant, and easy-to-clean materials to ensure long-term reliable operation. In order to adapt to different types and specifications of feed, feed processing machinery usually has adjustable functions, which can adjust parameters such as speed, cutting or extrusion strength during processing.
Because feed processing machinery often involves high-speed moving parts, operator safety needs to be taken into consideration when designing. This may include safety switching systems, protective covers, emergency shutdown devices, etc. When designing feed processing machinery, we usually pursue high efficiency and the ability to process a large amount of feed in a short time. This may involve optimized mechanical structure, efficient power transmission system, etc.
The ease of maintenance of the equipment is an important aspect of the design, including features such as ease of cleaning, ease of repair, and easy replacement of parts to reduce maintenance costs and reduce downtime. Some feed processing machinery may adopt intelligent and automated technologies to improve production efficiency and control accuracy. This may include automated control systems, sensors to monitor feed status, etc.
In some modern designs, considering environmental factors, the design of feed processing machinery may use energy-efficient technology, reduce waste generation, and materials that meet environmental standards. microswitches usually have a pair of electrical contacts that can be connected to a control circuit to achieve corresponding operations. This can be starting or stopping a motor, changing the operating status of a mechanical system, etc.
The microswitch has adjustable sensitivity and can be adjusted according to specific needs to ensure reliable triggering under different working conditions. IP67 microswitches for feed (grass) processing machinery are widely used in animal husbandry, breeding and other fields to control various processes such as feed mixing, transportation, and extrusion.